In Making Master Guitars, I used Mahogany or Spanish Cedar (Cedrela) for the neck – this being a commonly used species for many classical guitars. But now my preferred wood for the neck is walnut. It is harder and more dense than Cedrela and I like the beautiful patina you can achieve after polishing it. Most important though, is the hardness that makes it more effective at preventing energy absorption.
Tapered slots for wedges
After Jose Romanillos showed me his method of joining the sides to the neck with wedges inserted into tapering slots, I tried this out and was immediately converted. It is a much easier way of making a perfectly fitting junction between sides and neck, compared to the 1.8 mm saw cut slots that were in common use previously. (Although it it worth noting that the wedge method Jose himself saw on a very old guitar, so it is not new.)
Head veneer /facing
Where the head veneer meets the nut, a perfect right angle slot between the head veneer and the fretboard is needed, to hold the nut in place. Luthier Tony Johnson showed me his method (which differs from the one shown in my book). His is a better way of making sure the angle is correct before even gluing the head veneer on to the head.
What you do is place the head veneer on the head and project it a little way over the neck, so you can use a block plane on its side, laid on the neck, to plane the angle which will then be square to the neck.
To glue on the head veneer, you clamp a stop (I use a small engineer’s square) on to the neck, exactly at the change of angle between neck and head, and another stop at the far end, so the head veneer cannot move while being glued and clamped.
This avoids the need to cut the end of the head veneer later, when there is a danger of cutting into the neck surface.
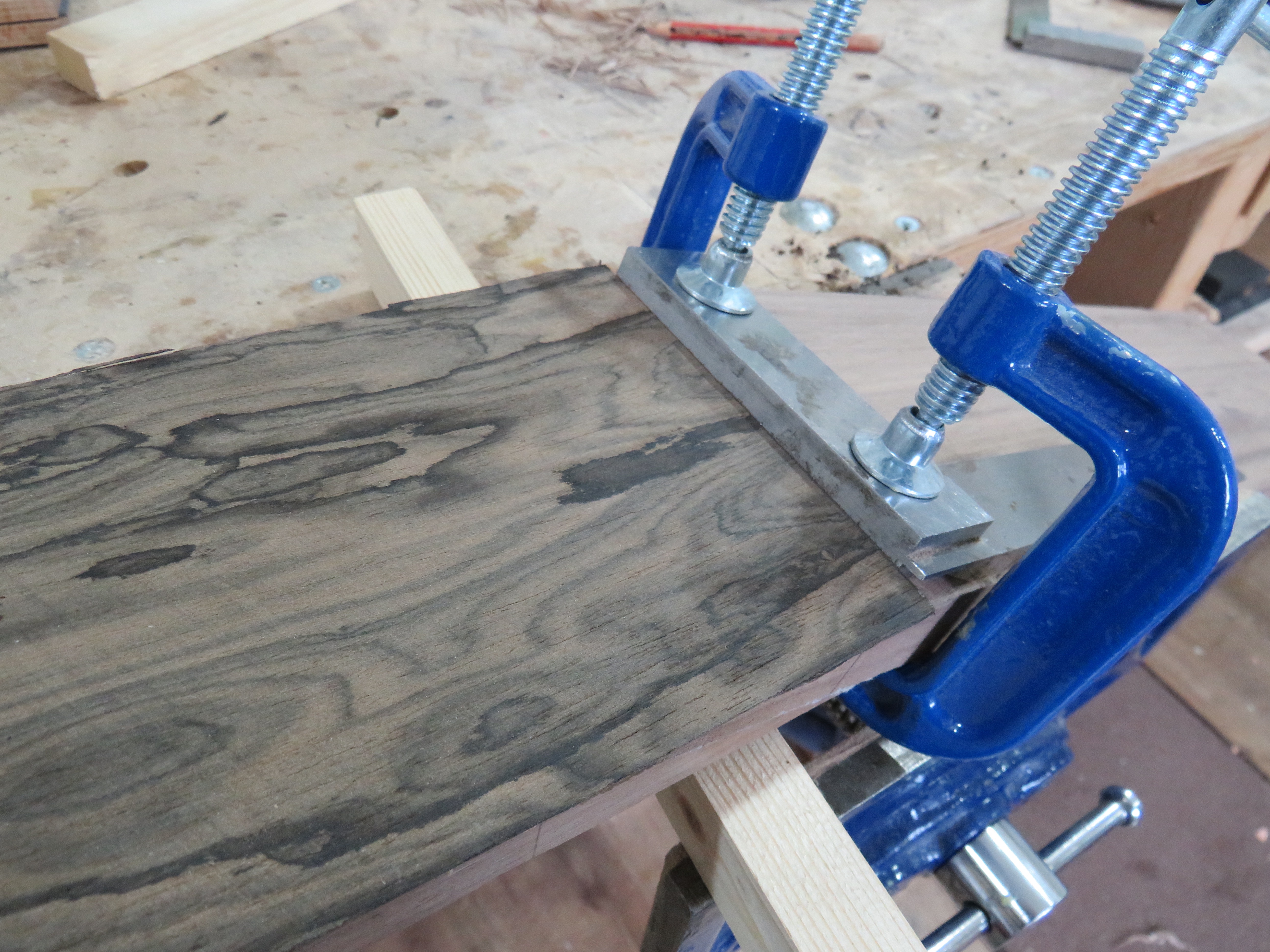
Machine Heads
Most tuning machines have 10mm rollers at 35mm centres. If the roller holes are drilled with a 10.5mm drill (or slightly smaller), a good fit will be achieved without the rollers binding. If they need cleaning out or reaming slightly larger, a drill bit held in a chuck can be used to fit them accurately.
When I studied with Richard Schneider in 1983, he was using wedges to attach the sides to the neck. He learned it from Juan Pimentel back in the 1960s. The difference is that he used spruce wedges.
That is interesting. But it seems more logical to use the same wood as the neck is made from. The wedge is simply a means of getting the rib securely into the groove. What is the virtue in using a softer species.
I would have thought that the wedge should have it’s grain running in the same direction as the heel. Somewhat harder to cut and it would need to o in sideways rather lengthways but would be less prone to differential movement issues.
Dave
You may theoretically be right but I don’t know anyone doing that. Actual fitting it would not be easy.
I’ve never noticed any movement issues. It is common in cabinetmaking to have one section joined to another with different grain directions.
Hello Mr courtnall.
Can you make an approach for guitars with elevated fingerboard?
I have not made raised fingerboards.
But I have made thick fingerboards about 8mm thick which is a little like a raised fingerboard.
Hi
What’s your view on V joints as a method for the head / neck joining?
Hi Barry
‘V’ joints are fine, if you like the look of them and the challenge of making a good one. You do need a thicker piece of wood than for a scarf joint. Most people seem to think the scarf is stronger, but I guess either joint, well-made, will last the life of the guitar.
My visual preference is for the clean lines of a scarf, which, if care is taken as to the cross-grain joint line, there is no visible joint. It looks almost like a one-piece neck, as in the beaufiful guitar I had as a child in the 1960s, made by the Dutch luthier, Jacob van de Geest, where the entire neck including the heel, was cut from one piece of Cuban mahogany.
Hi Roy
In his blog Joss sets up for a graphite tone truss rod.
Could I ask for more detail. Such as typical section size, type of fit in the slot, material for bonding it in.
Are you able to recommend a supplier?
Was this feature developed since your book was published?
Hello Andy, Joss here. I used ‘Graphite Tone Truss Rod Acoustic Classical Guitar 355 x 8.6 x 4mm’ from ToneTech suppliers. Rout a 10x5mm slot down the centre and bed the rod in rapid dry Araldite. Smooth it out over the top of the rod, so that you have a thin, smooth, level layer of araldite on the top. Don’t use too much araldite in the slot as it will squeeze out when you put the rod in. Good luck!